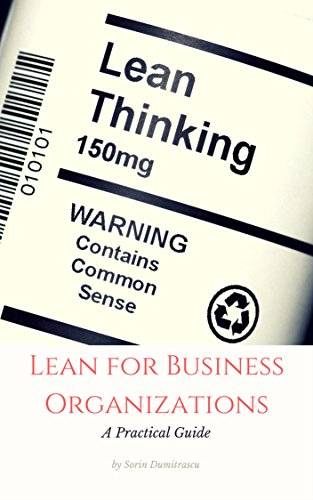
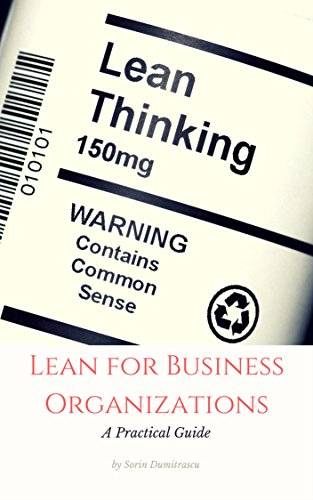
Lean for Business Organizations: A Practical Guide
by Sorin Dumitrascu
Using inefficient procedures is like digging a 200-foot wide hole for a 100-foot wide house. You'll have wasted a great deal of effort on something you don't really need. Your organization must make shrewd investments in its precious time, money, and effort. You need flexible, intelligent strategies to evolve and prosper in a competitive global market.
Lean is a methodology that incorporates a powerful set of tools and techniques designed to maximize customer value while constantly working to reduce waste. It focuses on improving overall efficiency, quality, and customer satisfaction.
Because of its ability to improve customer satisfaction and deliver bottom-line financial gains, Lean is a preferred strategic choice for many organizations. This course introduces you to the basic principles of Lean, which will help you create more efficient processes and get you on the road to successful operations management.
This course also outlines the five-step process for implementing Lean. By learning how to implement Lean in your organization, you can reduce the costs of developing your company's product, increase production efficiency, and improve safety, quality, and performance levels. Finally, the course explains how Lean integrates with the Six Sigma production management system. Using this hybrid approach enables you to minimize process and product defects, and to identify and resolve pervasive problems.
Today's markets are very competitive and customers insist on the best quality products for their money. This means that businesses must actively pursue perfection to keep their customers and to retain their market share. Pursuing perfection and excellent quality are important principles of Lean thinking. Continuous improvement, the elimination of waste, and striving toward zero defects all help organizations attract and keep customers, and so increase their profitability.
This course introduces four Lean tools organizations use to strive for perfection and improve quality – 5S, Hoshin Kanri, jidoka and poka yoke, and standard work. As you work through this course, you'll find out what these tools are, their purpose, and how the tools are used. You should then be able to recognize how the tools may be used in your own organization.
The course provides examples of how the Lean tools can be applied in both manufacturing and service organizations. It will help you assess your own organization's needs and determine how you can apply the tools to perfect what you offer.
How can you make your organization more efficient? The simplest way is to eliminate waste from your processes. This waste can be caused by many factors, such as untidy workspaces and surplus inventory. Or it might be caused by inefficient distribution of work. Using Lean tools, you can make your processes smoother and your workspaces tidier.
To implement a Lean solution, you must know what tools and techniques are available, and which ones would best help you. You have to select the best blend of Lean techniques for your organization. You can use a number of Lean techniques to make your organization run more smoothly. These include the visual workplace, just-in-time, kanban, and line balancing.
The visual workplace uses signs and other visual cues to convey information quickly. The visual cues include work instructions, process flow diagrams, and status boards.
Just-in-time ensures that you have exactly the right amount of supplies needed at any time. This helps to reduce surplus inventory. Kanban cards are triggers that alert the team to send more parts or supplies. The parts are then "pulled" into the system, based on demand. Line balancing results in the even distribution of work among workers. No workers are overburdened, and no workers are left idle. Using the Lean techniques outlined in this course will help you to develop strategies for improving flow and pull in your organization.
Lean is a methodology that incorporates a powerful set of tools and techniques designed to maximize customer value while constantly working to reduce waste. It focuses on improving overall efficiency, quality, and customer satisfaction.
Because of its ability to improve customer satisfaction and deliver bottom-line financial gains, Lean is a preferred strategic choice for many organizations. This course introduces you to the basic principles of Lean, which will help you create more efficient processes and get you on the road to successful operations management.
This course also outlines the five-step process for implementing Lean. By learning how to implement Lean in your organization, you can reduce the costs of developing your company's product, increase production efficiency, and improve safety, quality, and performance levels. Finally, the course explains how Lean integrates with the Six Sigma production management system. Using this hybrid approach enables you to minimize process and product defects, and to identify and resolve pervasive problems.
Today's markets are very competitive and customers insist on the best quality products for their money. This means that businesses must actively pursue perfection to keep their customers and to retain their market share. Pursuing perfection and excellent quality are important principles of Lean thinking. Continuous improvement, the elimination of waste, and striving toward zero defects all help organizations attract and keep customers, and so increase their profitability.
This course introduces four Lean tools organizations use to strive for perfection and improve quality – 5S, Hoshin Kanri, jidoka and poka yoke, and standard work. As you work through this course, you'll find out what these tools are, their purpose, and how the tools are used. You should then be able to recognize how the tools may be used in your own organization.
The course provides examples of how the Lean tools can be applied in both manufacturing and service organizations. It will help you assess your own organization's needs and determine how you can apply the tools to perfect what you offer.
How can you make your organization more efficient? The simplest way is to eliminate waste from your processes. This waste can be caused by many factors, such as untidy workspaces and surplus inventory. Or it might be caused by inefficient distribution of work. Using Lean tools, you can make your processes smoother and your workspaces tidier.
To implement a Lean solution, you must know what tools and techniques are available, and which ones would best help you. You have to select the best blend of Lean techniques for your organization. You can use a number of Lean techniques to make your organization run more smoothly. These include the visual workplace, just-in-time, kanban, and line balancing.
The visual workplace uses signs and other visual cues to convey information quickly. The visual cues include work instructions, process flow diagrams, and status boards.
Just-in-time ensures that you have exactly the right amount of supplies needed at any time. This helps to reduce surplus inventory. Kanban cards are triggers that alert the team to send more parts or supplies. The parts are then "pulled" into the system, based on demand. Line balancing results in the even distribution of work among workers. No workers are overburdened, and no workers are left idle. Using the Lean techniques outlined in this course will help you to develop strategies for improving flow and pull in your organization.
